In terms of food cold chains, an inability to provide an integrated cooling solution results in greater bacteria spoilage, higher rejection rates, and increased risk of contamination. As a result, 40-60% of estimated post-harvest food and fresh produce perishes prior to getting to market, with two-thirds of these losses occurring in the “first mile” from the farm. This amounts to 1.2bn tonnes of produce, which could feed 300m people (source: Food and Agriculture Organization of United Nations – FAO).
The World Bank estimates that reducing post-harvest losses by 1% would add a value of $40m per annum, the majority of which would accrue to smallholder farmers (source: Fund for Innovation & Development).
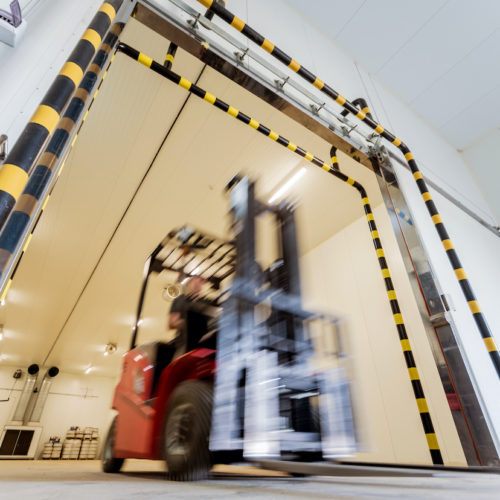
The cold chain is divided into four stages:
PIA Togo endeavours to create cold chain logistics in Togo to pursue the objectives such as:
- Reduction of food wastage and enhanced shelf life.
- Opening of opportunities for exporting local grown fruits and vegetables to EU, the USA and other countries under various special trade agreements.
- Employment opportunities and up skilling of human resource (in logistics, warehouse operation & maintenance and other associated services).
- In/directly contributing for the economy of the country.
- Health sector in Togo can leverage the warehouse facility to strengthen their supply chain and distribution operation.
- 10,000 sq.m. at PIA Adetikope and 2500 sq.m. at the airport.
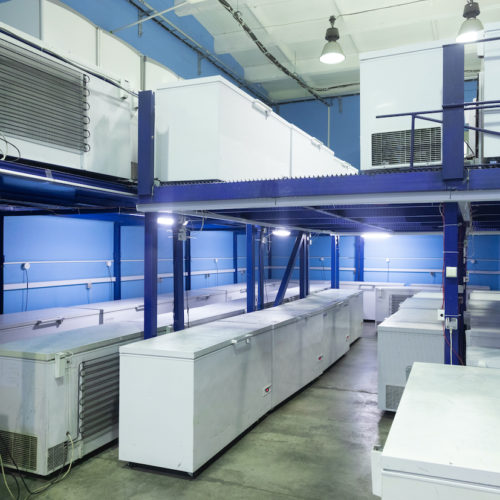
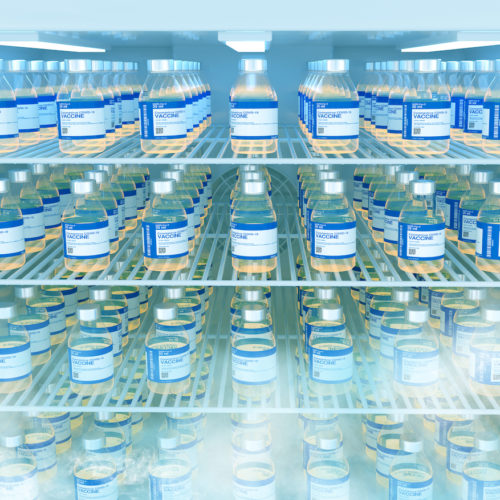
Above facilities would ensure:
- Growing retail sector in developing economies and growth of urbanization, digital e-commerce,
- To address global supply chain bottlenecks,
- Availability of emergency medical requirements, and
- Globalization in terms of trade and business opportunities for export.